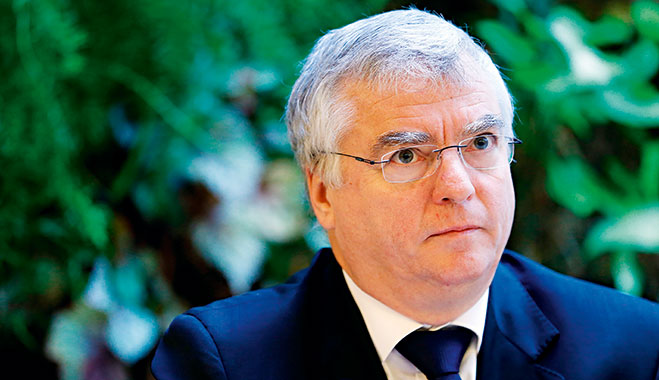
Such is the voracious appetite for paper of the world’s fastest-growing economy that China’s Nine Dragons – one of the most important Asian clients of French recycling group Paprec – will soon assume the mantle of the world’s biggest paper-manufacturing company. Nine Dragons has worked its way to the top by demanding the highest-quality raw material for its giant mills, something the French company is only too happy to deliver.
“Our quality must be beyond reproach, which is normal for us,” explains Stéphane Armange, Paprec’s Commercial Director for Recycled Paper. “We have never had a container returned from Asia.”
That’s quite a record for a company that first began developing links with Asian paper groups over 15 years ago, but it is exceptional in China where hawk-eyed customs officials have no hesitation in rejecting shipments of any kind of raw material they regard as sub-standard. It is by no means unknown for them to reject several thousand tonnes of recycled paper because it contains excessive levels of moisture or the slightest trace of putrescent material.
“If certain European countries sometimes sent suspect material to Asia in the past, it’s no longer the case now”, adds Armange. “The Chinese in particular have adopted western standards and will not tolerate sub-par consignments.”
Like other Chinese paper mills, Nine Dragons buys delivery contracts through Rotterdam-based agents who demand conformity to international standards. In Asia any product flaw may end in the withdrawal of that most precious of commodities, an export licence.
Exponential growth
As an operator of the most modern machinery available, Nine Dragons’ expectations mirror the goals of Paprec, which conforms to the highest benchmarks. According to Nine Dragons’ head buyer in Europe, Paul Moolenkamp, Chinese paper groups will import higher volumes of raw material from Europe provided they meet their increasingly stringent standards.
Half a billion books: Paprec’s European alliance
Nearly 15 years ago, a Europe-wide consortium of mainly privately owned book printers formed an alliance with Paprec that has endured and grown since. Known collectively as CPI, the consortium produces some 500 million books a year from 17 plants in France, UK, Germany, Switzerland, Spain, The Netherlands and the Czech Republic. All of these companies – some of which have been in business for centuries like France’s Firmin Didot group established in 1713 – have developed highly specialised, interlocking expertise that makes them unique in Europe. And they pool their expertise according to the often-challenging demands of publishers.
For example, if a publisher wants to capitalise on one of its authors winning a major literary award, it will arrange for the overnight production of 100,000 copies of a book that has been kept under wraps until the day of the announcement. If one printer cannot handle the entire contract, it will be shared out.
But in books, quality of production – and hence of the paper – is often paramount. According to Alain Cohidon, Chief Executive of CPI Aubin, the biggest book-printer in Europe, the relationship with Paprec is all about continual innovation. “As far as we are concerned, the collaboration with Paprec is built on confidence. They listen to our requirements and they understand the commitment to quality that unites all our partners in CPI”, he explains.
“Paprec was able to provide equipment and technology that was not only perfectly adapted to our needs but was capable of constant modification. That way, operating quality is guaranteed on a daily basis. The durability of our relationship is based on the fact that it has never stood still.”
“Nine Dragons operates on the highest international environmental metrics such the ISO 14001 standard”, he explains. “Logically, the company demands that the fibres it buys meet its requirements, which is to say beyond reproach and fully certified. And we know we can count on Paprec to guarantee this level of quality.”
Forget the paper-less office first espoused by Microsoft and other standard bearers for the new computer-driven world some 30 years ago. When current owner Jean-Luc Petithuguenin founded Paprec in 1994, it processed an annual total of 40,000 tonnes a year of what is technically known in France as FCR, recycled cellulose fibre. Today, after increasing volumes by a staggering 29 percent a year, the group reconstitutes no less than two million tonnes of FCR a year on top of other industrial waste.
In that time the sources of the material have multiplied. In the early days Paprec handled the paper created mainly by the printing, packaging and retail industries. Now some of its biggest clients are financial and government sectors.
The group, which is the biggest independently owned processor of industrial waste in France, operates a virtuous cycle in the case of the printed word. After the general reading public has dumped its newspapers, magazines and other written material, the Paprec truck collects the waste paper from recycling bins and other locations. All this material, mainly in the form of colour publications, is then sorted and transported by truck or barge to one of the group’s 30 processing sites in France.
There the paper is pulped, the cellulose fibres separated and the resulting mixture cleaned of all impurities in a highly technical process. Next, the ink is removed and the paper whitened. Finally, it’s cut into sheets, wound onto reels and returned to the printers in pristine condition, ready to receive the printed word all over again. Some 800,000 tonnes of the paper is exported around Europe and a further 400,000 tonnes to Asia.
Garnered development
One of the group’s not-so-secret weapons is its proprietary vacuum technology. An elaborate but robust system, it comes in the form of industrial-sized spiralled tubes, conveyer belts and elevators that are installed right alongside giant, high-speed printing machines and then lead to the outside of the plant.
The system captures vast amounts of the scrap paper that would otherwise fall by the wayside in the cutting and layout processes at the printing sites. Once the paper has been collected, it’s then compacted into space-saving packages for pick-up by trucks.
“We have no competitor at a technical level”, explains Wiliam Lebec, Paprec’s Commercial Director. “We start from the basis that the vacuums are the main element in the effective performance of the printing machines. They allow the printing companies to focus on what they do best.”
The technology is so superior in fact, that Paprec’s statistics show it wins 80 percent of bids to install the technology and as a bonus is often contracted to do the recycling too.
The technology was developed by the group’s R&D team first established a quarter century ago, and has been steadily refined ever since. It was the R&D unit that also devised a system for removing not only the air from the waste paper but the dust as well. Printing plants throw out vast amounts of dust, especially at the cutting stage; but what to do with the dust?
The team came up with another ingenious solution that compacts the dust into dense inflammable, wheel-shaped cakes. And to further speed up – and simplify – the process of reconstitution, the R&D team has refined the system further so the technology can be installed on-site. Indeed some 70 percent of the group’s French customers have opted for on-site dust separators and compactors.
The recovery of unused paper is almost an obsession with Paprec and it has found ways to collect it at every stage of the printing process. For instance, standard-sized skips often take up too much space at some of the smaller plants. The group has got around the problem by installing smaller, stackable pallets at crucial points along the printing presses. “It’s all about flexibility and robustness”, adds Lebec.
Publishing is a demanding industry that runs on the tightest schedule and delays in the printing process can have disastrous knock-on effects right down the distribution chain. That’s why, just in case something goes wrong, Paprec provides on-call technical service on a 24/7 basis for newspaper groups such as the Amaury Group that publishes and prints the top-selling daily Le Parisien.
“Quality of service has to be beyond reproach because the paper is printed seven days a week – and at night”, explains Lebec. “In these circumstances the equipment for capturing waste cannot suffer the slightest failure.”
In short, if the waste paper isn’t being collected, the printing machines cannot run as normal and schedules are in disarray.
Paprec has grown more or less simultaneously with the mounting pressure from government and local authorities as well as from the community at large to eliminate waste of all kinds including paper. Some of the group’s longest-standing relationships are with clients in Spain, where the Kimberly-Clark group is a shareholder, and in Germany, which practically pioneered the recycling of paper in Europe.
“The German industry had a belief in recycling before other countries and today is a producer at incredible levels,” points out Armange. As Nine Dragons’ buyer Paul Moolenkamp will vouch, Asia is following suit.